Definition of an LED Panel Repair Machine
LED displays have gained popularity in the past few years for various uses, like televisions, digital signage, and other applications. Nevertheless similar to any device LED displays may encounter issues. Stop functioning properly over time. In the past fixing LED panels required intervention from experienced technicians. With advancements automated machines, for repairing LED panels have been developed to simplify and enhance the repair procedures significantly.
An LED panel repair machine is a specialized automated device designed specifically for repairing malfunctioning or broken LED panels. These machines utilize precision technology to replace damaged components on the LED panel, restoring it to full working condition.
The main components of an LED panel repair machine include:
- Heating element – heats the panel to remove old solder and components safely
- Robotic arm – delicately removes the faulty LED chip and solders a new one in place
- Control panel – allows the technician to input settings and monitor the repair process
- Optics – high precision camera and microscope to view small components
- Clamps/stand – securely holds the LED panel in place during repair
Additional features can include:
- Chip recognition – automatically identifies the LED chip type and required specs
- Defect detection – finds the exact location of panel issues
- Temperature controls – allows precise heat adjustment as needed
- Calibration tools – ensures the robotic arm is properly aligned
- ESD prevention – stops static discharge from damaging boards
- Automated handling – automatically loads and unloads panels
Having the right combination of heating, optics, robotics, and controls is crucial for LED panel repair machines to function effectively.
How an LED Panel Repair Machine Works
The LED panel repair process using one of these automated machines is relatively straightforward.
First, the damaged LED panel is securely clamped into place on the repair stand. Vacuum suction cups often hold the panel firmly during repair.
Next, the machine heats specific areas of the panel through the heating element to melt the solder holding the components. Built-in cameras precisely target the heat to only affected solder points. The temperature is carefully regulated to avoid damaging other panel areas.
With the solder melted, a high-precision robotic arm equipped with micro grippers is used to gently lift out the defective LED chip. The arm can rotate and pivot to reach LEDs anywhere on the panel.
The robotic arm then retrieves a new replacement LED chip and solders it into place with guidance from the built-in camera and microscope optics. Advanced chip alignment tools ensure accurate positioning.
During the automated repair process, the technician monitors everything on the control screen and can adjust any settings like temperature as needed. Some machines offer fully autonomous repair capabilities once initialized.
Within minutes, the damaged component is swapped out and soldered into place, restoring function to the LED panel. The panel is then unloaded from the machine ready for re-installation.
Types of Damage an LED Panel Repair Machine Can Fix
LED panel repair machines can fix a wide variety of damage types, including:
- Dead or darkened LEDs – replacing bad solder connections and LEDs.
- Short circuits – resoldering wires/traces causing shorts.
- Backlight issues – soldering new CCFL tubes or LED strips.
- Component replacement – swapping out fuses, capacitors, etc.
- Connector issues – reattaching loose wire harnesses and cables.
- Broken panels – repairing cracks and severed circuit paths.
- Moisture damage – cleaning and reconditioning corroded areas.
In many cases, technicians will combine the automated repair machine with some manual rework for optimal results. But for issues like dead LEDs and shorts, the machines provide an efficient, high-quality solution.
Benefits of Using an LED Panel Repair Machine
There are many advantages to utilizing an automated LED panel repair machine rather than traditional manual repair methods:
- Faster repairs – Machines can repair panels in just minutes versus hours needed manually. Their speed and parallel processing abilities allow high volume throughput.
- Improved consistency – Repairs meet the same standards each time instead of relying on technician skills. Automated precision eliminates human variability.
- Higher success rates – The micro-level precision and tools of machines yield higher quality, long-lasting repairs. They minimize errors that could affect repair durability.
- Capacity increases – A single machine can handle repairs for multiple technicians’ workloads. Less manpower is needed compared to manual methods.
- Cost savings – Automated repairs can cost 60-70% less than full LED panel replacement in many cases. Labor and downtime are reduced as well.
- Better for the environment – Repairing panels prevents electronic waste and new component manufacturing compared to replacements.
For any repair shop, factory, or business that handles a high volume of LED panel repairs, utilizing an automated LED panel repair machine makes the process faster, more affordable, and more consistent.
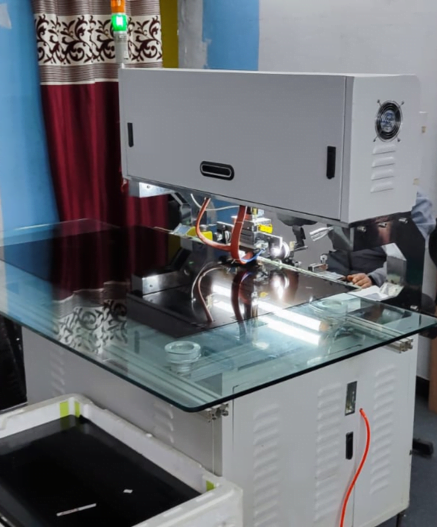
Limitations of LED Panel Repair Machines
While extremely useful, LED panel repair machines do have some limitations to consider:
- High upfront cost – The machines carry a large price tag, anywhere from $10,000 to $100,000 based on capabilities.
- Panel size restrictions – Larger TV-size panels often cannot fit in repair machines designed for smaller panels.
- Learning curve – Technicians need training to operate the machines and interpret results.
- Maintenance needs – Keeping the robotic arms properly calibrated and aligned is key for proper repairs.
- Limited reasoning – Machines can’t troubleshoot beyond what they’re programmed to fix and may miss nuanced problems.
- Manual repairs still needed – Very intricate panel issues require human skills and judgement for best results.
For less severe LED panel damage, manual repair remains a viable option. But when panels have significant damage, utilizing an automated LED panel repair machine is the most efficient method.
When to Use an LED Panel Repair Machine
Knowing when it is appropriate to utilize an LED panel repair machine is important for maximizing its value. While capable of fixing many issues, these machines are better suited for certain repair scenarios and damage types.
Moderate to Severe LED Panel Damage
LED panel repair machines truly thrive when addressing more significant panel issues. Their precision abilities allow reliable repairs on extensive damage not feasible manually.
If an LED panel has multiple dead LEDs, entire rows/sections not lighting, shorts across PCBs, or severe backlight/power issues, then the repair machine can quickly remedy these problems. The heating elements and microscopic soldering precision are tailored for this level of repair.
Technicians may be able to temporarily fix some moderate damage types manually, but the repair machine delivers more permanent, consistent fixes. Utilizing it on severely damaged panels also restores value compared to scrapping them.
High-Volume Repair Situations
When there is a backlog of damaged LED panels or a high daily repair volume anticipated, the automated machines maximize throughput and speed. Manufacturing facilities, repair shops, digital signage networks, and other operations handling LED panel repairs regularly can benefit most from the machines.
By offloading large amounts of repairs to the automated process, technicians’ workloads are lightened. Multiple machines can be implemented for additional scale as needed.
Cost Reduction Over Replacement
In many cases, moderately damaged LED panels would simply be replaced instead of repaired due to labor costs. However, an automated panel repair machine can reduce the repair expense below the price of replacement panels.
Factoring in labor savings and repair machine scale, costs can be minimized by 60-70% or more compared to new panel purchase and installation. This helps stretch value from existing panel assets vs unnecessary replacements.
Organizations aiming to cut costs through more affordable in-house repairs can justify purchasing a panel repair machine based on long-term savings. The initial capital expenditure pays back over years of intensive use.
For any situation requiring fast, affordable repairs on several damaged LED panels, implementing an automated repair machine boosts productivity and efficiency.
Steps to Repair an LED Panel with a Machine
While LED panel repair machines handle most of the intricate work automatically, technicians still need to follow an effective process to utilize them properly. Here are the typical steps to repair an LED panel using an automated repair machine:
1. Inspect the Panel and Identify the Problem Area
Thoroughly examine the non-functioning LED panel, testing voltages and signals to determine the malfunctioning component(s). Dead LEDs, backlight/power issues, and shorts will become apparent from panel inspection. Knowing the exact repair area allows better machine preparation.
2. Power Off Panel and Disconnect
For safety, completely power off the LED panel and disconnect it from any video cables, power cords, or mounts/stands. Removing power avoids electrical hazards for the technician and prevents shorts during the automated repair.
3. Secure Panel in Repair Machine
Most LED panel repair machines have panel clamps, stands, or vacuum suction cups to securely hold the panel. Ensure the damaged component side faces upward for access by the robotic arm. The panel must be fixed firmly to avoid movement during repair.
4. Input Repair Settings
Based on the inspection findings, input the required settings into the repair machine like the temperature, LED chip type, repair location coordinates, and more. Programming the correct parameters helps guide the machine during autonomous operation.
5. Activate and Monitor Automated Repair
With the machine settings configured and the panel loaded, activate the automated repair process. Monitor the control panel display as the heating elements activate, robotic arm solders and new components are installed. Tweak any settings if needed along the way.
6. Remove the Panel and Inspect the Repair
Once the machine completes the repair sequence, power down the system, remove the panel from the clamps and reconnect any cables. Thoroughly inspect and test the panel to confirm full function has been restored before putting it back into service.
With the right technician oversight and preparation, LED panel repair machines automate the intricate soldering and component replacement required to fix malfunctioning LED panels and restore them safely back to working order.
Choosing the Right LED Panel Repair Machine
Purchasing an LED panel repair machine represents a major investment, so it is important to select the right model suited for your repair facility’s needs. The key factors in choosing an effective automated repair machine include:
Repair Volume
Consider the typical daily and monthly LED panel repair workload to handle. Higher volume operations need more production capacity. Evaluate if a single machine can fulfill demand or if multiple units are required.
Panel Sizes and Types
LED panels come in a wide range of dimensions from small indicator panels to large TV sizes. Ensure the repair machine can accommodate the panel sizes needing repair. Also account for differences like edge-lit vs direct-lit backlight designs.
Handling Fragile Panels
Thinner or brittle LED panels require very gentle automated handling. Choose machines with vacuum or foam padding clamps to avoid panel cracks or scratches during the repair process.
Range of Repair Capabilities
Assess if a machine can handle all the LED panel damage types and components needing repair. More advanced machines offer wider repair flexibility.
Speed and Throughput
When high volume throughput is essential, machines with faster heating tools, multi-arm robots, and automated load/unload panels maximize productivity.
Control and Monitoring Features
Machines with intuitive control screens, camera displays, and software to monitor repairs in real time provide helpful feedback to technicians. Advanced analytics capabilities also optimize the repair process.
Calibration and Maintenance
Look for calibration tools and software to properly setup, align, and maintain the robotic arm for consistent performance. Regular calibration prevents positional drift.
Manufacturer Reputation and Support
Established manufacturers with proven reputations for high-quality machines and support deliver better ownership experiences. Look for responsive technical support and available spare parts/consumables.
Costs/Budget
Machine costs range widely from around $10,000 for basic single-arm tabletop units to over $100,000 for sophisticated multi-arm production systems. Compare costs to the value delivered from repair savings and capabilities needed.
Carefully weighing all these aspects helps identify the right LED panel repair machine or machines suitable for an operation’s requirements and budget.
Types of LED Panel Repair Machines
There are a few main categories of LED panel repair machines to consider:
Entry-Level Repair Machines
Ideal for smaller repair shops, entry-level machines provide a lower-cost way to automate basic LED panel repairs. They typically feature:
- Single robotic arm with limited range of motion
- Smaller desktop size and repair area
- Basic heat plate for soldering
- Minimal control panel and manual load/unload
While lacking some capabilities, these affordable machines can handle common repairs like LED replacement for smaller LED panels.
Advanced Repair Machines
With more features and higher capacities, advanced machines offer greater repair versatility for larger operations:
- Dual-arm or multi-arm robots
- Larger chamber sizes for bigger panels
- Precision heating lasers
- HD cameras and microscope viewing
- Automated panel loading/unloading
The expanded functionality allows efficient, high-quality repairs on a wider scope of damage.
Commercial Repair Systems
The most heavy-duty repair solutions are commercial systems built for factories and large-scale production:
- Industrial six-axis robotic arms
- Customizable chamber sizes
- Multi-zone heating plates
- Centralized computer control
- AI-powered defect detection
- High-level automation
Maximizing throughput and first-pass repair success, these powerful machines streamline repairs even on severely damaged panels.
The optimal repair machine class depends on factors like repair volume, panel sizes, budget, and features needed. With the right selection, an LED panel repair machine can provide an excellent return on investment through substantial process improvements.
Safety Tips for LED Panel Repair Machines
While automated machines enhance the safety of LED panel repairs by handling dangerous soldering tasks, technicians should still follow important safety measures when using this equipment:
- Wear protective gloves when handling panels after heating – surfaces stay hot for some time after machine repair.
- Ensure the repair area/room has adequate ventilation – the heating elements produce heat that should dissipate.
- Follow the manufacturer’s recommended safety guidelines for operation and maintenance.
- Keep hair, clothing, and jewelry away from the moving parts of the robotic arm.
- Handle panels carefully when loading/unloading to prevent cracks or breakage.
- Confirm panels are firmly secured in clamps to avoid movement and slippage during repairs.
- Only qualified technicians should operate the machines after proper training.
- Routinely check for detached wires, damaged cords, or other electrical hazards.
- Power down and disconnect the machine before any maintenance or servicing.
While LED panel repair machines contain many inherent safeguards to protect users and panels, practicing safety first helps avoid accidents and injuries. Consult the manual and manufacturer for further device-specific guidance.
Common Repair Machine Issues and Troubleshooting
Like any complex automated equipment, LED panel repair machines can encounter technical issues needing troubleshooting. Here are some common problems and potential solutions:
Panel Overheating
If the solder is melting in incorrect locations or the panel gets too hot, adjust the repair profile temperature settings downward incrementally. Use the lowest heat necessary for the repair.
Robotic Arm Calibration Issues
Over time, robotic arm joints can lose positional accuracy. Recalibrate the arm/grippers following the procedure in the device manual. Calibrate anytime repairs seem off.
Loose Panel Clamping
When the repaired panel shifts during the process, inspect the stand clamps/vacuum and replace any worn clamping pads. Keep fasteners tight. Clean vacuum cups regularly.
Unresponsive Control Panel
Try rebooting the repair machine and its software if the control panel or displays freeze. If the issue persists, contact technical support for assistance. Updates may be needed.
Diagnostic Error Codes
Consult the user manual and troubleshooting guide based on any error codes shown. Codes indicate certain malfunctions needing correction. Contact technical support for help if errors persist.
Troubleshooting repair machines promptly preserve uptime. Maintain the equipment according to manufacturer guidelines for optimal performance.
Automated LED Panel Repair Innovation
As LED panels continue growing in prevalence, demand for automated repair solutions will also expand. This will drive further innovations in the technology:
Expanded Self-Diagnostics
With more onboard sensors, next-gen machines may perform automatic diagnostic tests identifying exactly which components need replacement before repairs begin.
Improved AI Integration
Smarter machine vision and artificial intelligence programming will allow fully autonomous analysis and repairs with less technician oversight needed.
Enhanced Precision
Robotics and manipulation systems will gain abilities to handle tinier components and solder joints, expanding repair possibilities.
Larger/Faster Machines
With optimized heating, clamping, and motion systems, panel repair machines will scale up for very high volume throughput.
Specialized Panel Fixtures
Dedicated fixtures customized for LED TVs, digital signage, automotive displays, and other panel types will simplify repairs.
Remote Monitoring/Control
Cloud-based monitoring and controls will allow remote machine optimization, troubleshooting assistance, and software upgrades.
Mobile/Portable Machines
Compact mobile panel repair systems will bring automation capabilities directly onsite to installations.
The efficiencies and capabilities of LED panel repair machines will continue accelerating as technology progresses. But even today’s solutions deliver tremendous advantages for the repair process when utilized properly.
Conclusion
LED panel repair machines provide transformative benefits for the repair of malfunctioning or damaged LED panels. By automating intricate soldering and component replacement, the machines fix panels faster, more affordably, safely, and consistently than manual repair methods.
Operations handling high daily panel repair volumes can improve productivity and quality greatly by incorporating these automated systems into their workflow. The machines handle repairs beyond the scope of manual work, restoring value to severely damaged panels.
With capabilities spanning from entry-level machines for basic LED replacement to industrial-grade solutions for large operations, panel repair automation is scalable for many repair scenarios.
When choosing a machine, factor in panel sizes/volumes, repair types, precision needed, and production goals. With training and proper use, technicians will maximize the advantages of automated repair automation.